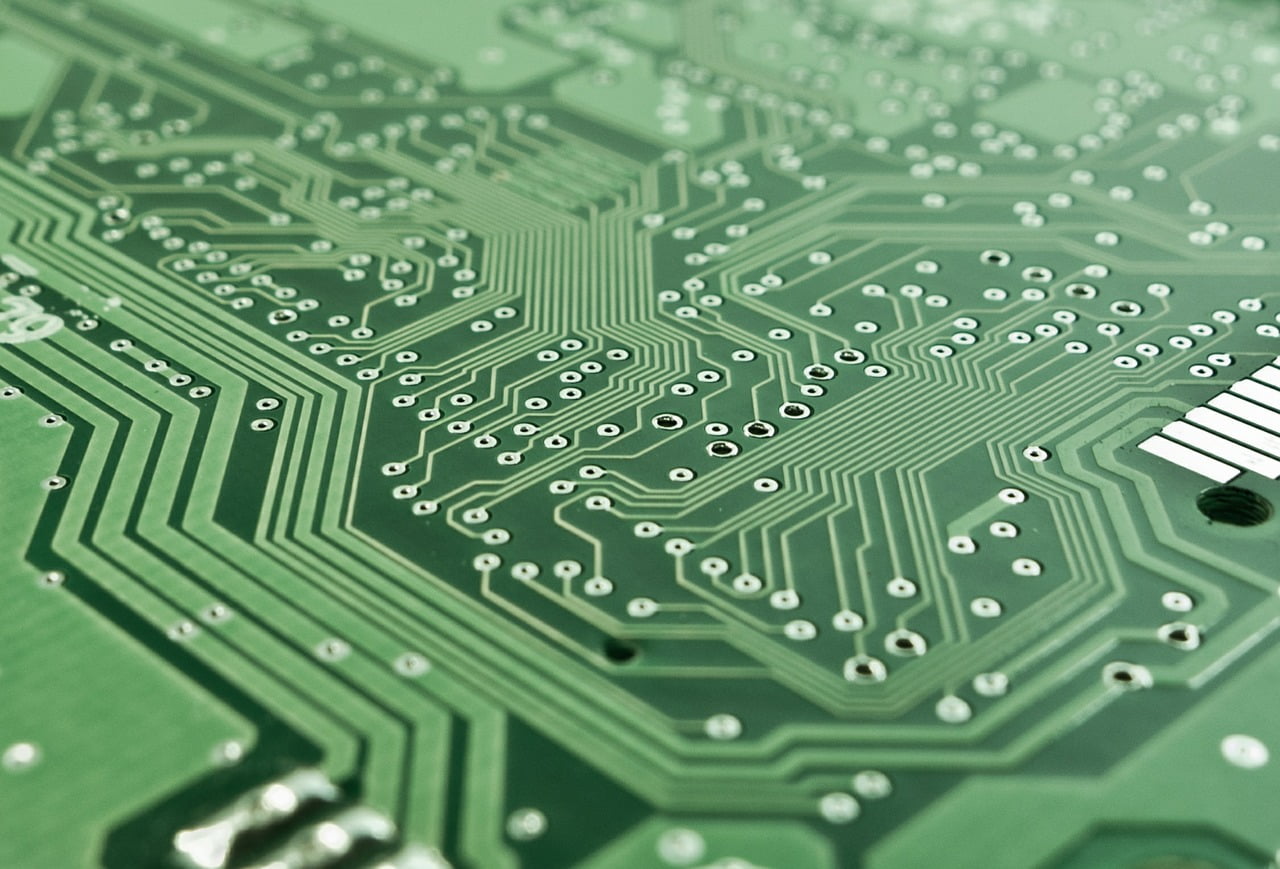
As you already know, PCB (Printed Circuit Board) production is a complex and nuanced process entailing meticulous planning and execution by skilled workers and machinery. In this manufacturing and assembly process, one of the most important instances is quality control. Inspection is a vital part of PCB production from the earliest stages all the way to the finished product, yet there is only so much the human eye can keep track of at the same time.
This begs the need to introduce a more effective and efficient control method such as AOI (Automated Optical Inspection) that can alleviate the pressure of such a nuanced task, and expedite the entire process from start to finish. Here are the five reasons why automated optical inspection should be a vital part of PCB production.
A new level of accuracy
The human eye is a magnificent product of nature, boasting a resolution as powerful as a 576 megapixel camera and the ability to see much further than Earthβs five-kilometer curvature. But machines are better, at least when it comes to the efficiency of data configuration and processing. While it might take the human brain far more energy to process visual information and act on it, AOI can enhance the level of accuracy while remaining consistent and efficient throughout the process.
Essentially, this means that although visual inspection is still an integral part of the process, AOI can elevate the level of precision and catch every defect, no matter how miniscule it might be. This becomes extremely important in fixing errors promptly before the unit moves on to the next stage of the production process.
Increased inspection speed
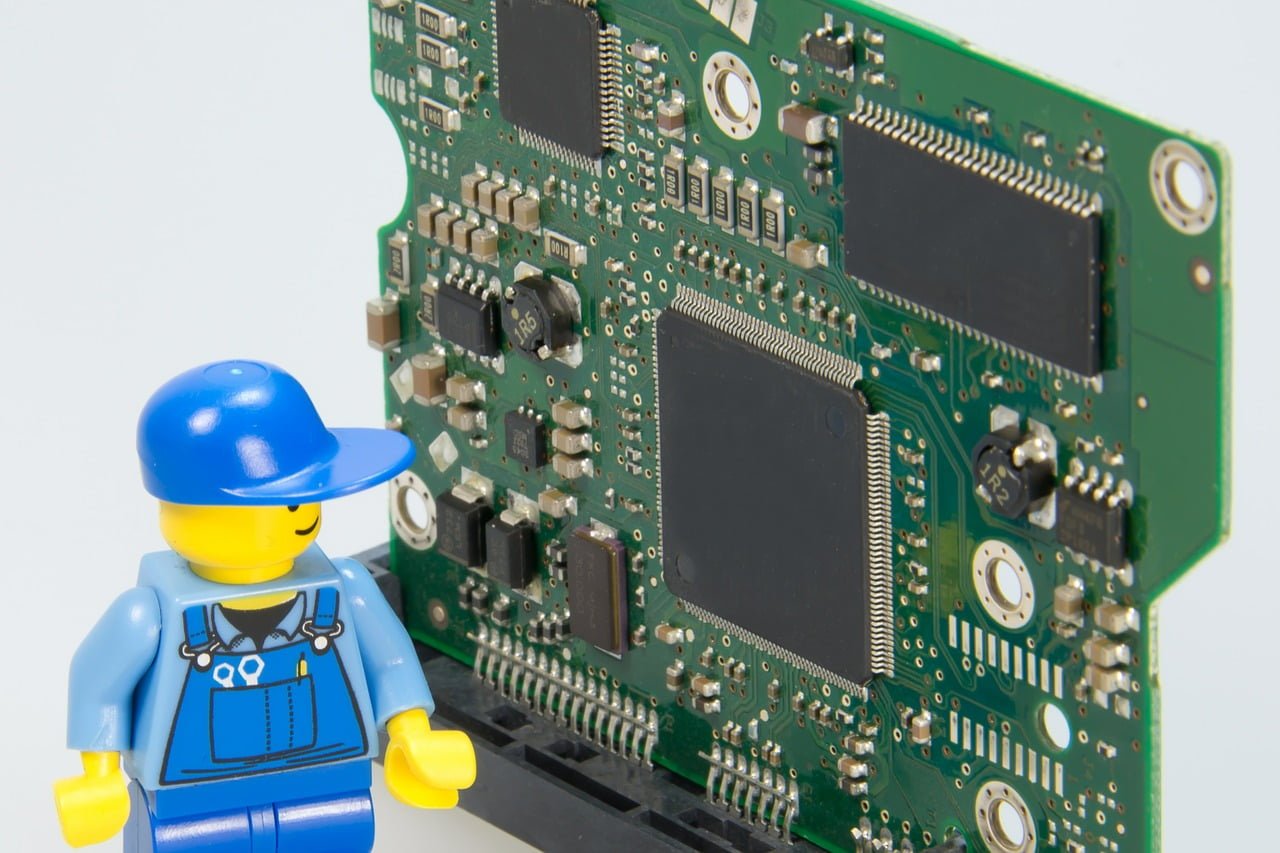
Whereas the human brain will oftentimes sacrifice efficiency for the sake of accuracy, AOI machines are able to maintain high levels of accuracy without hindering processing speed. In a nutshell, these machines are extremely quick, and if handled properly, they can knock hours off the entire process.
Provided that the machine is properly programmed and tuned for a specific task, what should have been an hour-long visual inspection can now be a quick minute-long automated process. When the machine has finished reporting the bugs, it will be up to the operator to validate or disprove these errors, which will also take a fraction of the timeframe needed for manual inspection.
Ensuring inspection consistency
One of the biggest problems for OEMs and EMS companies is ensuring consistency during the inspection process from start to finish and throughout the product line. Given the fact that high volumes of PCB units might roll through the production process in a day, a reliable electronics manufacturer must implement AOI systems that can guarantee every PCB is up to the latest IPC class requirements.
Achieving this using traditional methods such as visual inspection is simply not feasible, which is why AOI and x-ray solutions have become the foundation of a successful PCB production line. Minimizing the risk of human error is paramount in these kinds of processes, and the AOI system aims to eliminate it altogether.
Eliminating errors as they occur
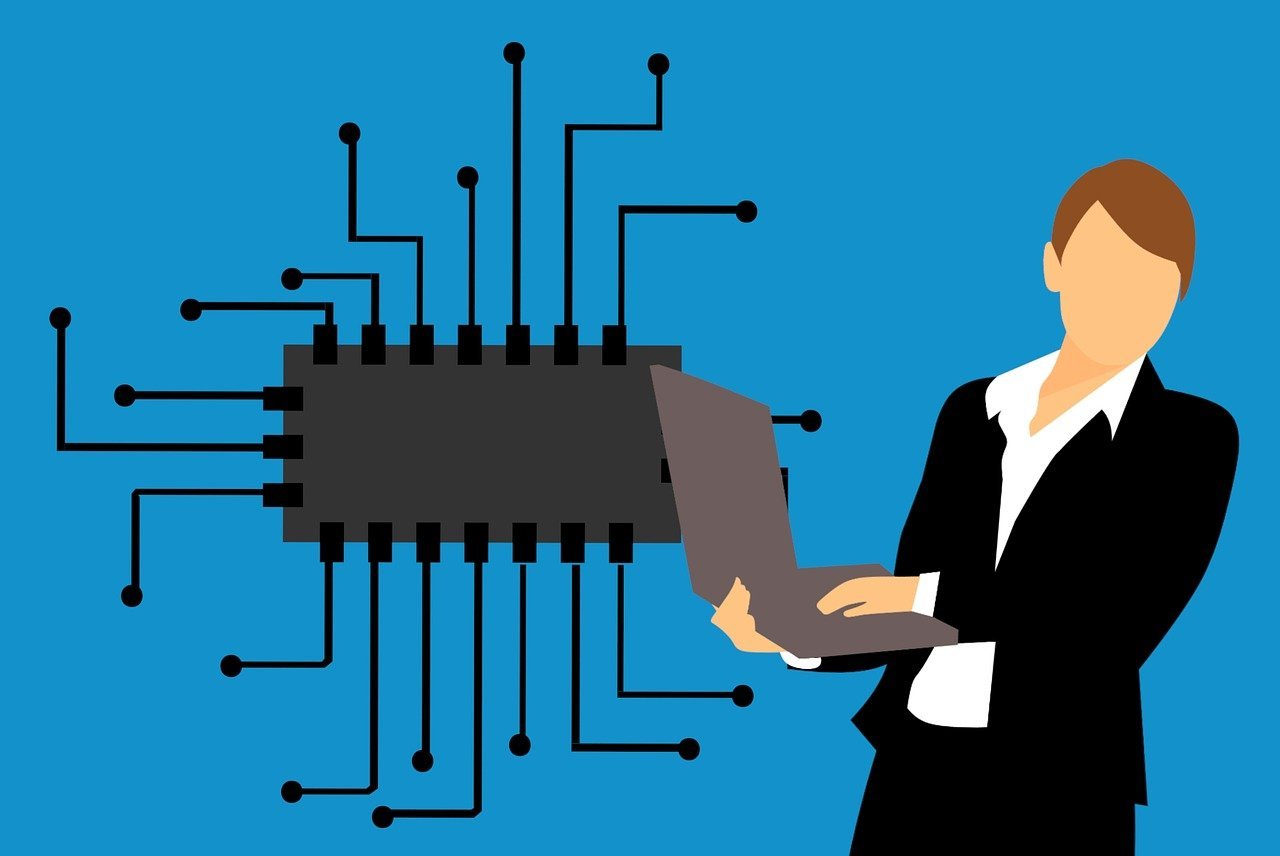
Speaking of eliminating human error, the fact still remains that errors are bound to occur during the production process one way or another. Whether the operator missed a defect or the machine malfunctioned for a fraction of a second, AOI systems are there to remedy the problem promptly and effectively.
Discovering a problem in the early stages of the production process is extremely important for the elimination of costly reworks down the assembly line, as well for ensuring the entire batch is free of any similar defects. This allows the AOI operator to communicate any issues with the SMT (Surface Mount Technology) line and help fix any problems before the product reaches the latter stages.
Reducing workload while increasing productivity
All of the above ties in seamlessly with the fact that AOI can effectively relieve the stress and the strain from the entire PCB production process. By catching errors and defects with speed and accuracy, these systems can prevent costly and time-consuming rework, and allow the product to move through the assembly line quickly. In turn, this will help keep visual inspectors βin the zoneβ when bigger problems occur.
PCB production is a nuanced process and modern businesses are using sophisticated inspection methods to meet the ever-increasing industry standards and deliver a better service to their customers. While visual inspection is still a vital part of the entire process, AOI systems have taken the task to a whole new level of efficiency and efficacy.